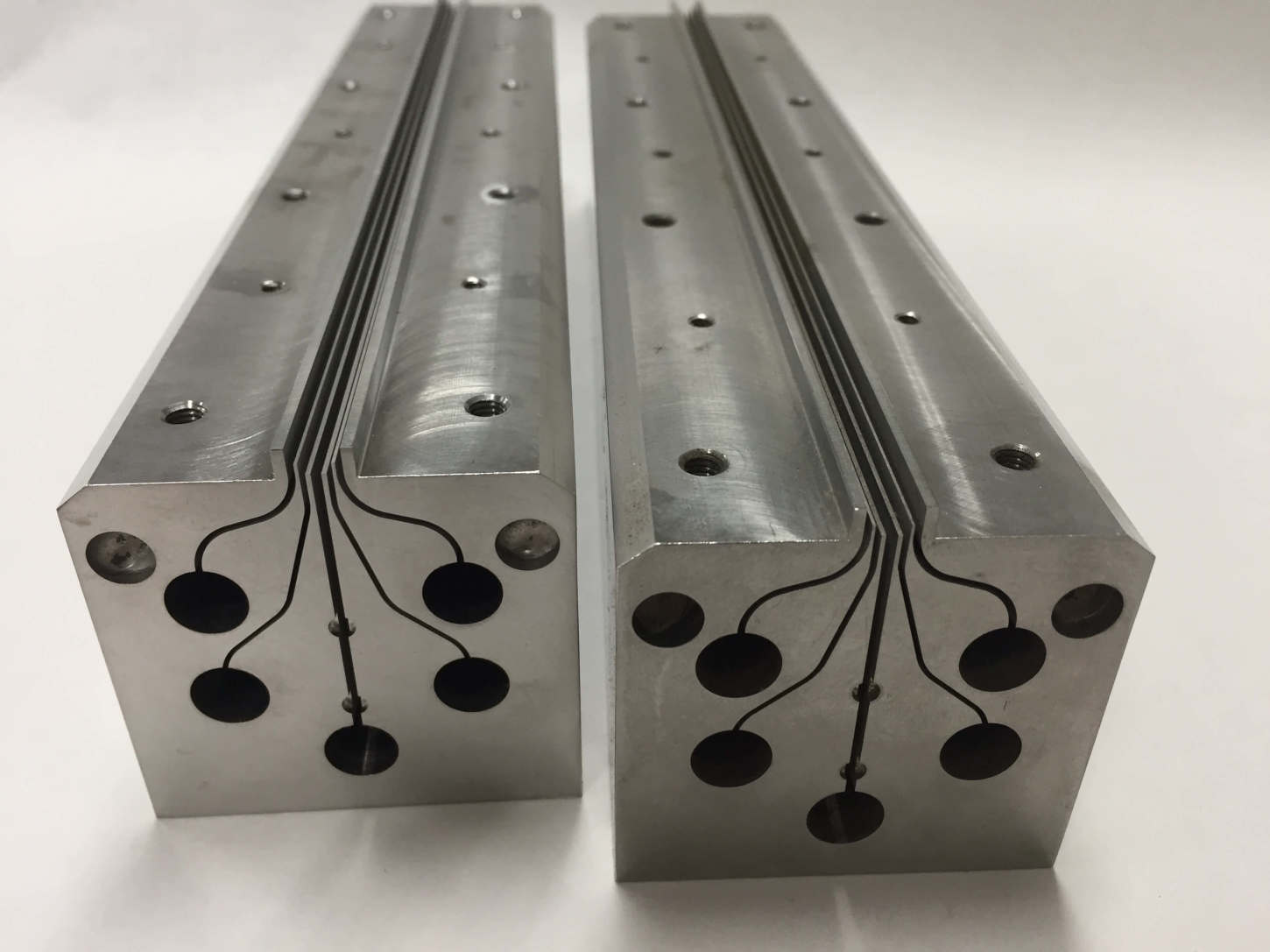
Wire electrical discharge machining is a method used to cut materials that are electrically conductive. An electrical discharge is produced between the wire and the conductive material being cut. This then generates sparks that swiftly and accurately cut through the material. Wire EDM can be used to create prototypes, limited production runs and multiple production parts. Creating a blueprint for new projects requires a huge amount of time and capital. This is because the prototype created must reflect the elaborate details outlined in the original design. To ensure that any model you create imitates the original specifications, it is crucial to use the Prototype Wire EDM . Again, this decision can warranty you very many benefits.
The first benefit is that wire EDM enhances precision and accuracy. When cutting conductive metals, wire EDM is the most reliable method for creating delicate and technical components. When using other machining types, clients often compromise on the accuracy since errors must be made. However, this is prevented when using EDM. Some prototypes may not work even when a small curve is not implemented using the right measurement. Through electrical discharge machining, every fine detail is implemented. It is important to note that complex technical procedures can only be accurately carried out through discharge machining. Hence, if you want a definitive prototype, you should definitely use this method of machining. Because of the extreme accuracy associated with wire EDM, production parts can be produced the first time correctly. This eliminates the need for follow-up.
The other crucial benefit of wire EDM is that it enhances high efficiency and swift turnaround. When creating prototypes, specific deadlines must be met. This is because investors and stakeholders might be waiting to see the prototypes in a meeting scheduled at a specific time. That being said, a tight schedule must be followed when developing presentable models of future products to show investors. Wire EDM offers the fastest rates of turnaround without compromising the quality of the final product. With wire EDM, you can easily get a product from the prototype stage to the actual market.
Electrical discharge machining requires minimal tooling procedures. This increases the levels of efficiency achieved throughout the entire process. Most methods used for producing prototypes follow old procedures that may take hours even to set up. With wire EDM, the time needed for set up is very minimal. This ensures that the turnaround time is very fast. In a case where you are producing long tapers, wire EDM is the best manufacturing method to use. Increased repeatability is another added advantage of wire EDM machining. This form of machining can produce delicate parts in different quantities. Therefore, if you want one or millions of parts, they can be produced using this method because the process is repeatable. By choosing to use wire EDM, you can easily produce internal cuts that are square-edged. This is impossible to achieve when using other machining methods. Additionally, this method can create extremely tiny holes that are difficult to produce when using other machining methods.